In Good Hands: The Art of Building a Snowboard
All snowboards are made by hand.
The fact is, unless it’s an extruded piece of plastic snowboard found hanging next to tennis rackets, miniature soccer nets and the latest soon-to-be busted yard game of the season, every snowboard is made by hand. That’s not just a Burton Snowboards thing either; that goes for pretty much anyone making legitimate boards. And while that hasn’t been thoroughly, thoroughly fact checked by a global factory audit, if there’s a mechanized method of building the best snowboards you can, it would have likely been developed – and in operation – at Craig’s, Burton’s R&D facility located in Burlington, Vermont.
The process – called layup – is one of the highlights of our public tours. Late spring and early summer is one of the prime times to catch it live, as we add a short production run to build limited models of our Backyard or Family Tree collections. The tour often likens board building to sandwich creation … which is by no means a slight, since nearly any respectable human being without a gluten issue has a deli they hit when it’s time to get real.
And like that deli, you can follow them to the market and go pick for pick on ingredients, but they still make it better. It’s called experience. And that’s what you see at Craig’s.
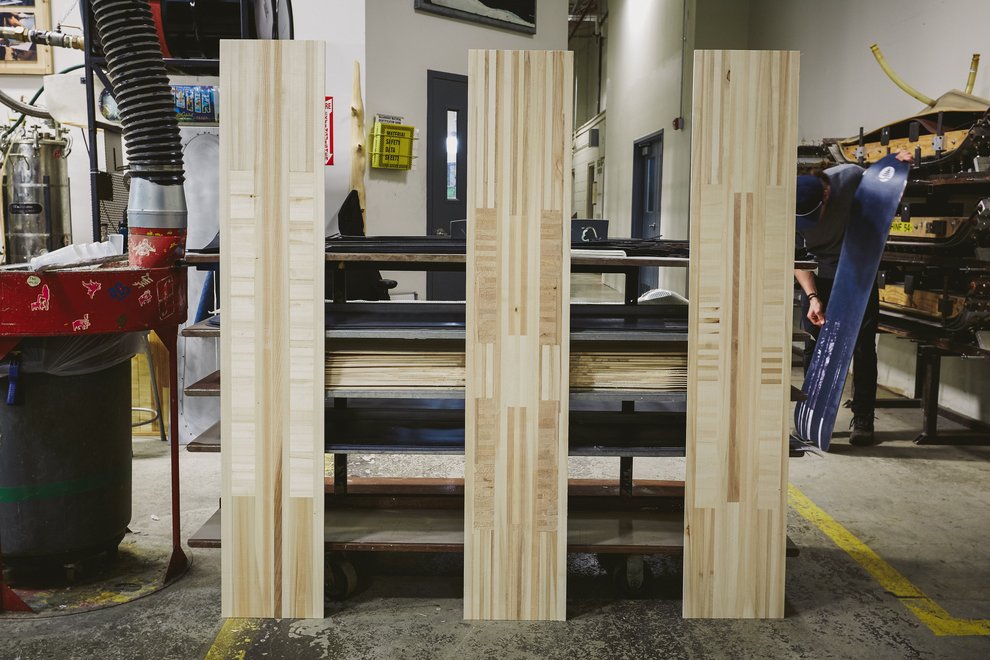
If a core is the meat of a sandwich, different types change the flavor of the ride. Burton has five FSC™ certified cores we like to use in the line. More expensive doesn’t mean better, ala roast beef vs. ham. It’s preference.
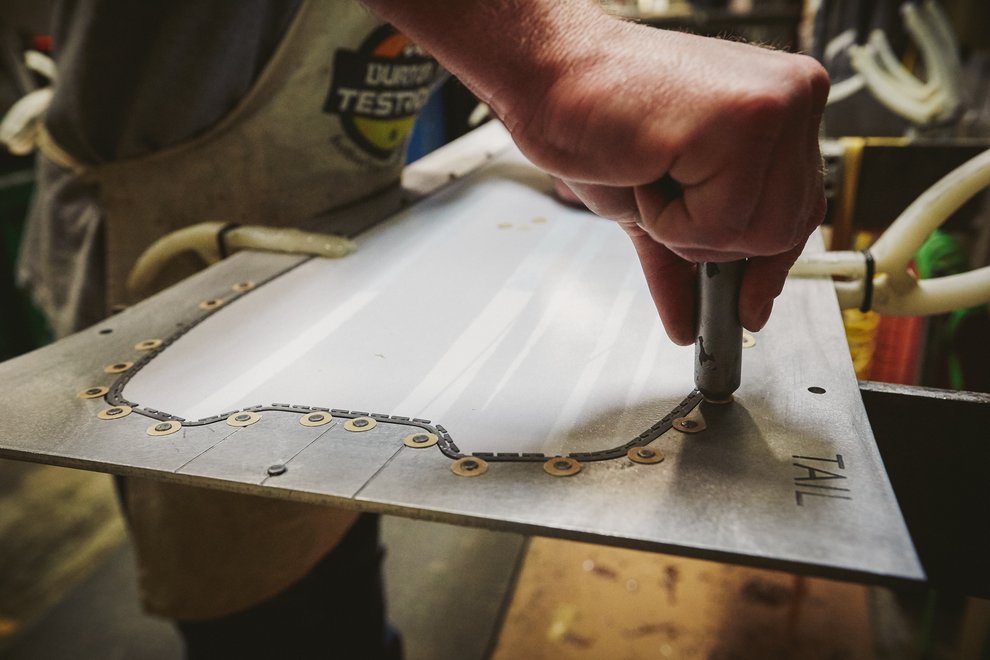
With the aluminum mold, the cut-to-shape base is down first, followed by edges trimmed and held in place. Base material ranges from fast and furious to long-haul durability – the bread, if you will.
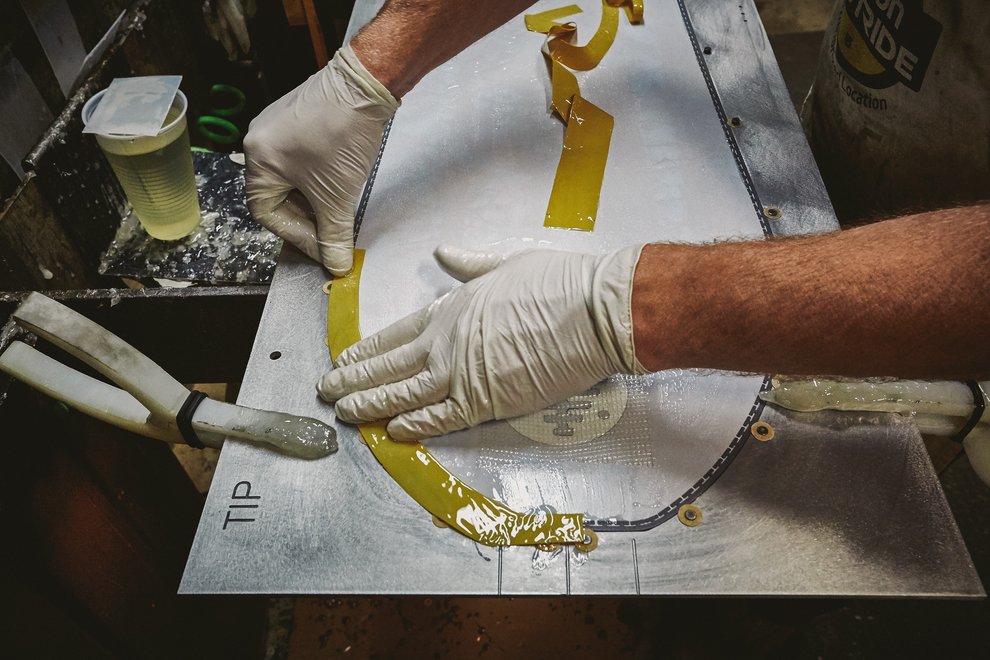
Strips of gummy paper help metal bond. In this case it’s the edges prepped for incoming layers.
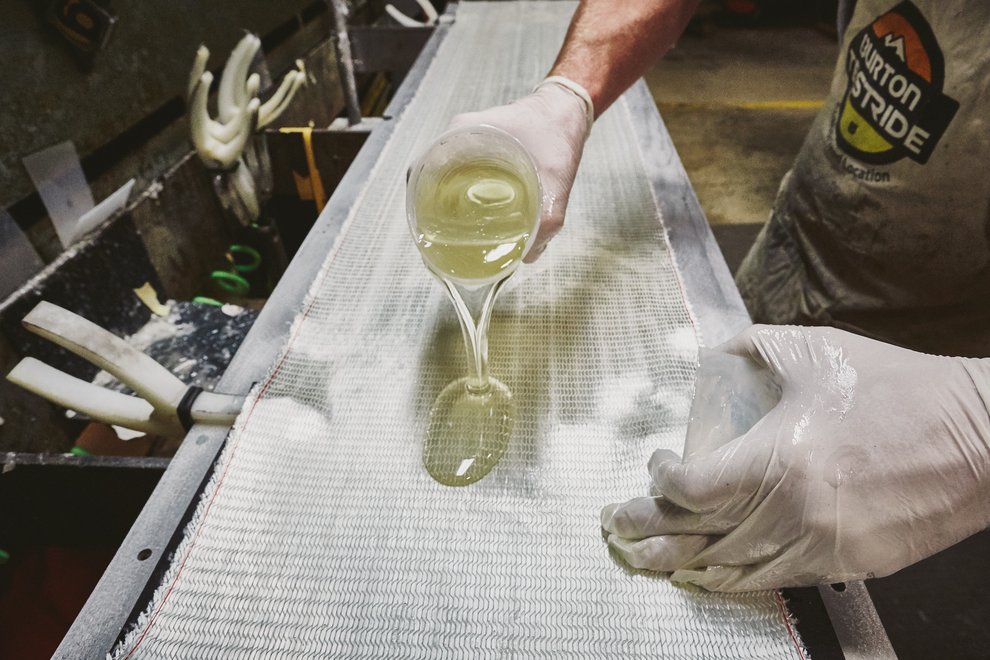
Fiberglass makes up two layers of the snowboard with the wood core in the middle. The variations in “the glass” seem infinite when even the direction of the weave affect the ride. Add strands of carbon and things get even more tasty, depending what you like. If a core is the meat, the glass represents cheese and condiments.
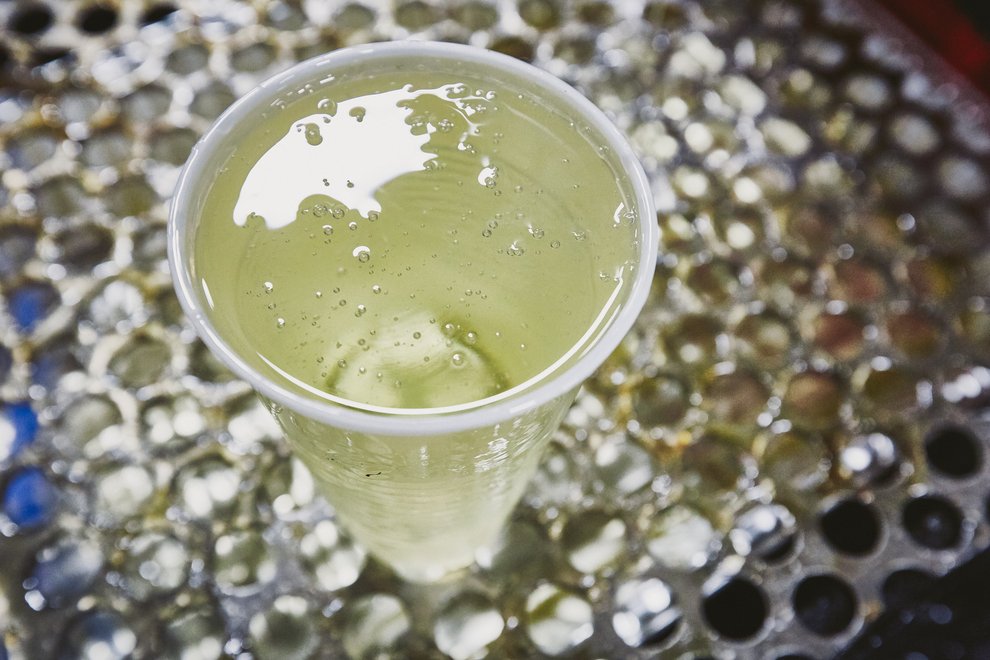
Between each and every layer is a hand-spread measure of epoxy. Over the past few years Craig’s has been testing the longevity of bio-based eco-friendly epoxy and introducing it to production. More than just glue, it brings a snowboard’s strength and character to life.
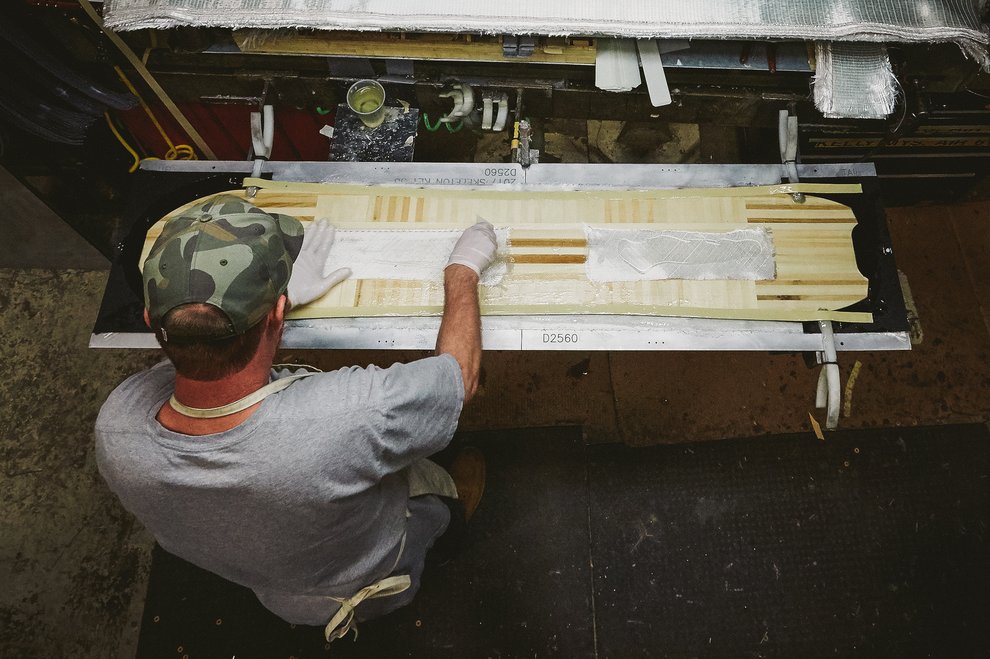
The core matches with the shape of the mold before layup. It’s been shaped and it’s been profiled for thinner and thicker sections (e.g. Pro-Tip™, Squeezebox, Off-Axis Squeezebox, Filet-o-Flex). The pattern in the wood is engineered grain direction, or EGD™ – just another variable.
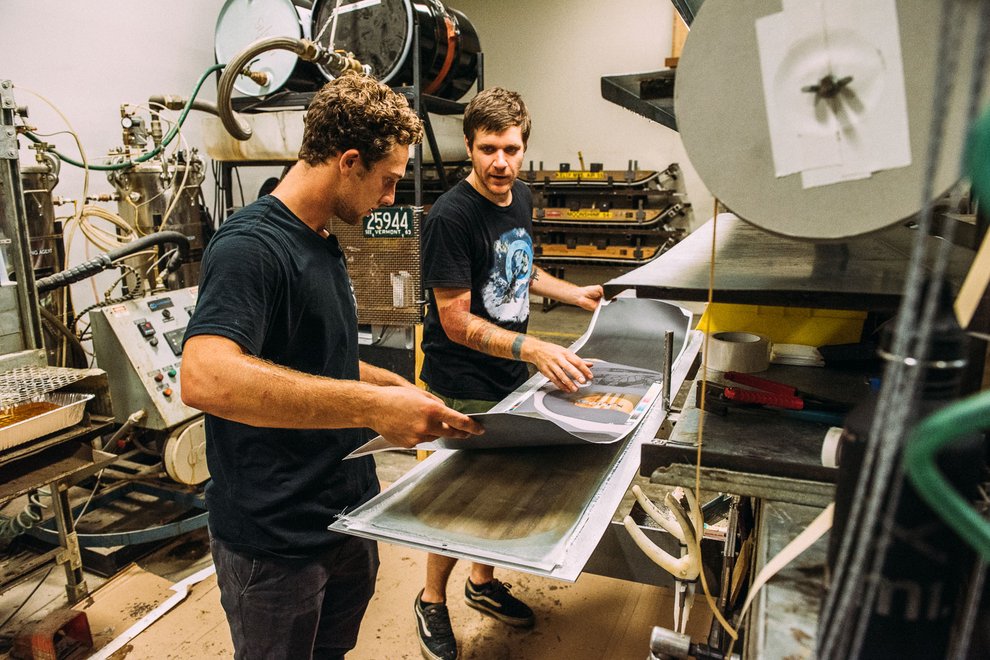
After the second layer of glass is down (hardly visible once epoxy has been spread), the top sheet is ready. Although not the most tech piece of the process, it’s arguably the most important when it’s time to choose. Don’t deny that.
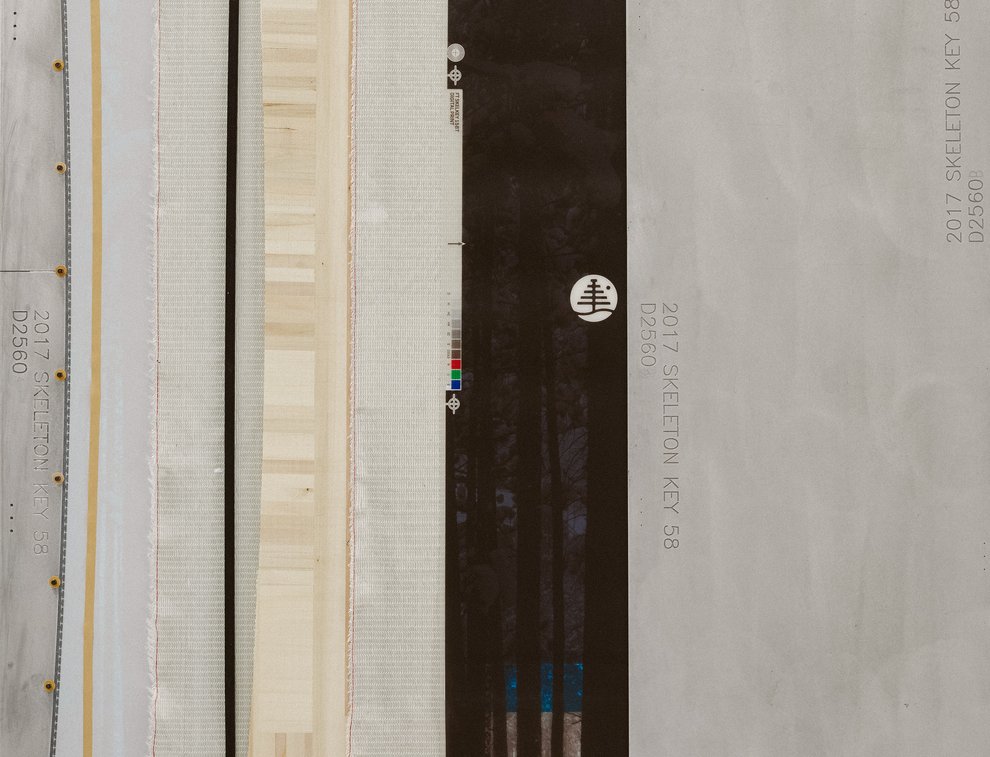
Altogether from bottom to top. The aluminum mold has a lid to seal it up before the board goes to the press, where heat and pressure will act as the grill. The camber of the snowboard will take shape there.
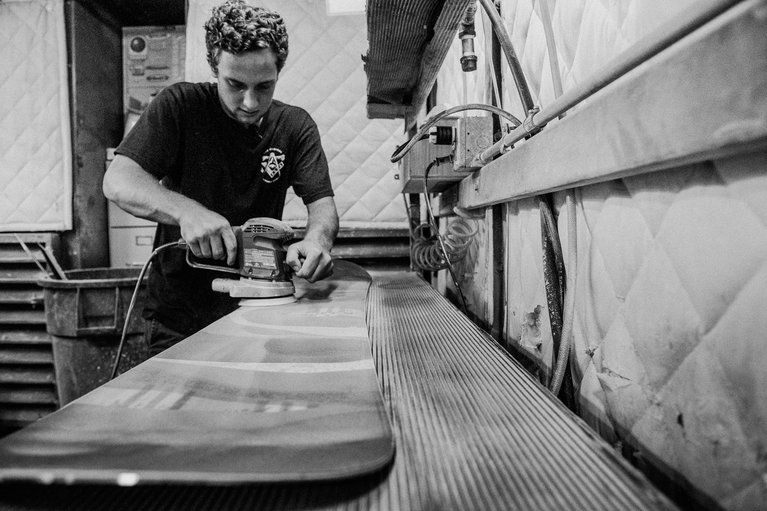
While Craig’s is more focused on perfecting and testing than mass production, a solid craftsman can turn 25 boards a day in layup. Give or take. While the process is quite repeatable, the variables play a significant role – and the people behind them understand what a little more spice can do to change a board’s flavor.
After all, it’s truly in their hands. Each and every one.
Touring Craig’s: Burton’s R&D prototype facility is the world’s premier facility for engineering and designing the future of snowboarding gear. Free tours offered daily and you can sign up online or check out this virtual tour of Craig's below: Click and drag left and right to look around, navigate using the portals at the bottom, and click the icons to learn more. Be on the lookout for some misty surprises we left for you to find.