Protecting Our People: Burton's Supply Chain Program is Now Accredited by the Fair Labor Association
Following a three-and-a-half-year journey, we are happy to announce that Burton’s supply chain social responsibility program has been accredited by the Fair Labor Association (FLA).
FLA accreditation is the gold standard for a systems-level approach to human rights compliance and social responsibility, recognizing that a company understands the consequences of its business practices on workplace conditions and has comprehensively implemented systems to successfully uphold fair labor standards in its supply chain. Accreditation requires companies to meet benchmarks that fully align with the International Labour Organization, UN Guiding Principles, and the Organization for Economic Co-operation and Development.
Our company has evolved considerably over the past 43 years. While we’re still headquartered in Vermont and focused on sharing snowboarding with as many people as possible, we have grown into a global brand powered by nearly 1,000 employees with the unified goal of helping customers get outside and experience the spirit of riding year-round. Our product line has expanded to include gear that supports snowsports and the mountain lifestyle–from Anon helmets and goggles to Burton boards, boots, bindings, outerwear, apparel, packs, and even camping equipment.
With growth comes complexity. Burton has developed international operations as a brand, retailer, and snowboard manufacturer. We have also established partnerships with factories around the world to produce our broad range of products beyond boards. Particularly in the textile industry, the prevalence of unethical conditions in factories is well documented and heartbreaking. We, as a brand, want to affect positive change for our people, our factories, and create ripples in the industry as a whole by trying to fix a broken system.
Rather than avoid challenges or disengage, we choose to lean in as global citizens and use our business as a force for good.
Burton fights for the rights of people around the world. During the last decade, we committed to reviewing the social and environmental impacts within our own supply chain and continue to make meaningful improvements.
In 2012 we established the Burton supplier Code of Conduct – the principles which all manufacturing partners must uphold if they want to do business with us. We audit suppliers according to strict social responsibility standards in order to understand the greatest risks that factory workers face and to establish corrective action plans for suppliers’ practices. Over a five-year period, we made difficult decisions to end relationships with nearly half of the factories we had previously partnered with, driven in part by their inability or unwillingness to meet Burton’s social responsibility standards.
We’re committed to cultivating long-term, healthy, transparent supplier relationships which place people and planet at front and center. We help suppliers build toward best practices to protect factory workers, human health, and the environment. We conduct trainings when significant issues are found, support factory-specific sustainability projects, and host biennial supplier summits to reaffirm our brand commitments and expectations.
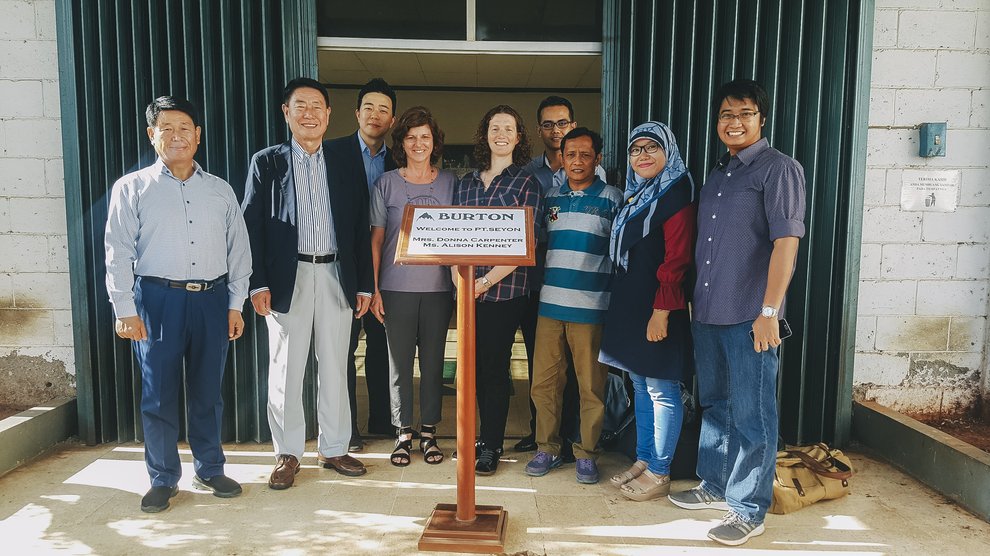
We also recognize that our own sourcing practices can influence workplace conditions. Supply chains are complex, which means that there is no single approach to responsible purchasing. We engage in open dialogue with all suppliers and solicit anonymous feedback to understand how we can progress our practices to promote productive relationships that result in increased worker wellbeing. This work is constant and ever-changing due to a variety of factors including shifting customer demand, trade policy, and unexpected crises like the COVID-19 pandemic.
While we have built strong relationships with suppliers, Burton is rarely a major customer for an individual factory, representing less than 20% of volume for more than 80% of the factories manufacturing our products. This means that in order to promote the well being of the roughly 75,000 workers employed by our suppliers, we have to work collaboratively to create change at the industry level.
Burton became a participating company of the Fair Labor Association in 2016 to support our commitment to ensuring safe conditions, ethical treatment, and fair labor practices throughout our company and supply chain. The FLA promotes and protects workers’ rights and improves workplace conditions by monitoring adherence to rigorous labor standards and facilitating collaboration among businesses, civil society organizations, and colleges and universities.
FLA accreditation is a major accomplishment that Burton is incredibly proud of, but this work is never finished. We are committed to continuous progression in our supply chain practices to improve the wellbeing of all workers that make our products. Success in sustainability means moving the benchmark forward for ourselves and across the industry.